
Simulation of Droplet Microfluidics
Designing droplet microfluidics has become a considerably complex task. The resulting designs are usually validated by fabricating a prototype and testing it with physical experiments. In case that the functionality is not implemented as desired, the designer has to go back, revise the design, and repeat the fabrication as well as experiments. This current design process based on multiple iterations of refining and testing the design produces high costs (financially as well as in terms of time).
On this page, we provide a method developed at JKU to overcome this “trial-and-error” design approach by means of sophisticated simulation methods. To this end, we first introduce the developed droplet simulator; afterwards, we summarize its application in a case study, which demonstrates the gained benefits. Moreover, in order to allow interested researchers and designers to quickly try the proposed simulation methods, we additionally provide an online version of our tool which provides limited features but showcases the capabilities of the approach.
Munich Microfluidics Toolkit (MMFT) Droplet Simulator
Simulations on the 1D analysis model (also called the electrical circuit duality) allow to validate the specification of microfluidic networks before any prototype is fabricated. More precisely, these simulations allow to predict e.g.
- the droplets' paths/trajectories through the network (this can decide which assay is executed on the droplet),
- the flow changes caused by all droplets and the resulting impacts (e.g. distance changes between droplets, droplet patterns, etc.), and
- the time a droplet takes to pass through the network.
Here, we are introducing our Droplet Simulator which
- directly works on the specification of the design and considers the interdependencies caused by all droplets,
- extends the current state of the art with important physical phenomena which are required for practical designs,
- is publicly available https://github.com/cda-tum/mmft-droplet-simulator.git (an online version of the tool is also available below), and,
- due to the availability of the source code and the event-based algorithm, can easily be extended to support further applications.
The simulator’s features can exemplarily be observed in the shown video, which shows the graphical output when simulating the trapping well presented in https://doi.org/10.1039/C7RA02336G. On the left side of this video, the graphical output of the simulation is shown which shows the droplet positions. On the right side of this video, the simulation is compared to a physical experiment. Therefore, we used images of a physical experiment captured with a frequency of 50 fps. When comparing the simulation with the experiment, we can observe equal droplet trajectories as well as similar droplet speeds and residence times.
Details of the Droplet Simulator are summarized in the article entitled “MMFT Droplet Simulator: Efficient Simulation of Droplet-based Microfluidic Devices” (https://doi.org/10.1016/j.simpa.2022.100440). An online version of the tool is also available below.
Furthermore, an older version of this simulator can be found at https://arxiv.org/abs/1810.01164, where the implementation (including a README with instructions) can be downloaded by clicking on this link (17 MB).
In case of questions/problems, please contact us through microfluidics.cda@xcit.tum.de.
If you use the implementation for your research, we would be thankful if you referred to it by citing the following publication:
@article{fink2022mmft,
title={MMFT Droplet Simulator: Efficient Simulation of Droplet-based Microfluidic Devices},
author={Fink, Gerold and Costamoling, Florina and Wille, Robert},
journal={Software Impacts},
doi={10.1016/j.simpa.2022.100440},
year={2022}
}
Case Study
In a conducted case study, we showed how a significant amount of the prototyping costs can be avoided when applying simulation before the first chip is fabricated. To this end, we demonstrate how the Advanced Simulation Framework described above can help in the design process. Therefore, we compare the design process with and without using simulation. As a case study, we use a microfluidic network presented in https://doi.org/10.1039/C7RA02336G.
This network is capable of trapping and merging droplets with different content on demand. The case study demonstrates how simulation can help to validate the derived design by considering all local and global hydrodynamic resistance changes. Moreover, the simulations even allow further exploration of different designs which have not been considered before due to the high costs.
Details on the case study are provided in the paper entitled “Simulation Before Fabrication: A Case Study on the Utilization of Simulators for the Design of Droplet Microfluidic Networks”.
If you are interested in setting up a simulation of your microfluidic design, please contact us through microfluidics.cda@xcit.tum.de. We are always interested in exploiting the potential of our simulator.
If you use the research, we would be thankful if you referred to it by citing the following publication:
@article{grimmer2018simulation,
title={Simulation before fabrication: a case study on the utilization of simulators for the design of droplet microfluidic networks},
author={Grimmer, Andreas and Chen, Xiaoming and Hamidović, Medina and Haselmayr, Werner and Ren, Carolyn L and Wille, Robert},
journal={RSC Advances},
volume={8},
number={60},
pages={34733–34742},
year={2018},
publisher={Royal Society of Chemistry}
}
Online Tool
In order to allow interested researchers and designers to quickly try the proposed simulation methods, we additionally provide an online version of our tool. Although this tool only provides a limited set of features (e.g., traps are not supported yet; we are working hard to implement corresponding GUI elements for those missing features), microfluidic devices composed of different channels and pumps as well as working with different fluids can already be designed and simulated by some few clicks.
The online tool also allows you to save and load your designs to be simulated. If you like, you can also try out the simulator with some test-files prepared by us which you can download by clicking on this link.
In case of any questions and/or problems, please contact us through microfluidics.cda@xcit.tum.de.
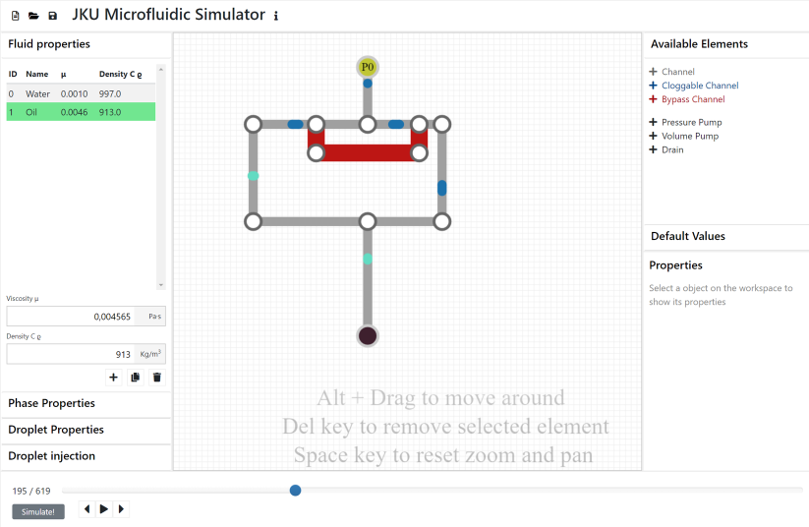
More on our work on microfluidics is summarized in this page.